Automation and Electrical Systems
Inicio » Business Areas » Automation and Electrical Systems
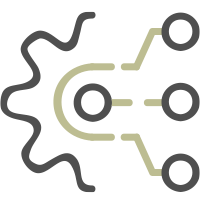
Automation
and electrical
systems
- Automation engineering and consulting
- Control systems engineering and GAMP
- Electrical engineering
- Communication networks and DCS solutions
- Integration of MES/MOM and Batch systems
- Cybersecurity
- Robotics and computer vision
- Digital twin
Automation engineering and consulting
Eigra Group's automation department consists of certified personnel in 'Wonderware Archestra' with industrial field experience for the development of SCADA applications and programming of PLCs, HMIs, and industrial networks and servers. This department provides the group with the capacity to design and manage all types of control and automation requests for any process within the industry. Along with quality control and project monitoring, the group ensures the client's confidence in the programming and process engineering and its status at all times. We assist our clients in analysing the needs of their facilities to enhance productivity, quality, and safety in their production processes.
Control systems engineering and GAMP
Eigra Group has qualified and experienced personnel in process system programming and SCADA applications. The development utilizes software from Siemens, Schneider Electric, Omron, Allen Bradley, Beckhoff, Wonderware (System Platform), inTouch, WinCC, and RSView, among others. Additionally, the group has a structured database of program blocks and documentation that outlines and details the development of programs or applications. This creates a concise and similar framework across all projects, saving development and production costs. We bring expertise in data transfer or exchange technologies such as OPC UA servers or IoT, including their design and implementation.
We allocate the necessary resources in all phases of an automation project according to GAMP standards (Good Automated Manufacturing Practice), FDA Part 11 compliance, and ISA-88 Batch Control.
Electrical engineering
Eigra Group's electrical department's experience combines with the team's skills for the development of electrical engineering for any industrial or tertiary process. Additionally, Eigra Group has a certified team in the development of schemes using 'EPLAN' and 'See Electrical Expert,' with a solid foundation and a standard procedure for generating schemes and reports that facilitates the study, manufacturing, and assembly of cabinets, as well as electrical installation and its proper execution. This procedure lays the groundwork for commissioning the installation, committing the group to its responsibility for the project.
Communication networks and DCS solutions
The design and selection of different types of industrial networks for an installation are fundamental when efficiency, control, and maintenance of the system are required. For each installation, and according to defined parameters (security, transmission speed, robustness, and network management through software), the industrial network is selected and designed to have a greater amount of data. We have experience in:
- Networks with AS-i, Profinet, IO-Link, Ethercat, Ethernet, Modbus RTU and TCP/IP, and Sinaut protocols.
- Use of hardware from Cisco, Siemens, Schneider, Wago, Hirschmann, and many other well-known brands in the industrial and tertiary sectors.
- DCS systems from leading manufacturers, including design and commissioning phases. Hardware configuration and control strategy programming.
Integration of MES/MOM and Batch systems
Manufacturing Execution Systems (MES) have evolved from both technical and functional perspectives, driven by new needs in the global economy. From the beginning, the MES system connected the informational or business management layer with plant operations. The goal is to achieve comprehensive production management.
Eigra Group offers the integration and implementation of plant operations and acquired data with its ERP business management systems and communication with customers or suppliers, among others. This is done through a wide variety of technology available in the market, tailored to the installation and the functional automatic system in the plant. In this way, managers can have complete, accurate, and real-time information about everything happening in the plant.
Tracking and controlling raw materials, process instructions, finished products, shipping, etc., are key aspects to achieve continuous improvement. This is achieved through traceability and batch recording to ensure strict manufacturing planning and regulatory requirements, based on the specific needs of each client.
We use leading software tools in the market for Batch process control in all types of installations and for any need, regardless of complexity.
Cybersecurity
Thanks to its experience in the industrial sector, engineering, and installations, Eigra Group identified the need to incorporate a cybersecurity service that supports industrial automation from the outset.
Working remotely is becoming more common, so effective remote management and proper data acquisition are essential for processing in control centers located at strategic sites. This "data transmission through the cloud" and plant control require specialized teams and a network architecture and programming based on security, blending hardware and software elements simultaneously.
Eigra Group leads this solution with a team specialized solely in this field and direct support from other departments within the group. Among the projects carried out with this solution, Siemens and Fortinet are the most commonly used, with the capability to adapt this technology to more potential clients.
Robotics and computer vision
Due to the demand from key clients, Eigra Group is responsible for the design, installation, and commissioning of any type of industrial plant or process line. This responsibility equips the company with the ability to design using artificial vision and end-of-line technology, enabling direct traceability and no loss of information under any circumstances or communication failures.
These technologies improve productivity, speed, quality, reliability, and flexibility to the maximum extent. Along with proper advice and the contribution of Batch or MES technologies, process times are optimized with real-time data acquisition.
On the other hand, the pursuit of quality is reflected as one of the fundamental standards of any industrial process and is positioned as one of the primary needs. Therefore, Eigra Group studies and designs solutions with software and artificial vision that allow real-time data acquisition and evaluation, enabling instant decision-making and improving process efficiency.
Digital twin
The digital twin is presented as a technology for simulating and analyzing industrial processes, capable of demonstrating and encompassing all the possibilities of the actual process. It is a completely digital representation and direct simulation of any type of element, process, or instrumentation that makes up a factory or station.
With real-time information from the plant, recorded history, and maintenance data, along with proprietary applications based on machine learning, it is possible to obtain an exact and precise model whose behavior and operation are identified with the real system.
Thanks to this, we achieve a protected and fully editable, simulated, and secure environment for experimentation and changes, with the possibility of detecting preventive problems, planning minimal maintenance downtime (they can even be avoided), simulating new operating standards by modifying setpoints or equipment, and more.
In this environment, it is not only necessary to design and simulate equipment and processes but also data, whether generated by the simulated application itself or collected in real-time from the production line.
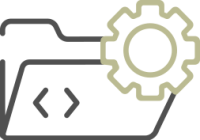